UTchem™
Corrosion-resistant process applications
Oilpeak is dedicated to enhancing various technologies, focusing on the application of corrosion-resistant materials in both dry and wet etching processes. These materials demonstrate excellent and stable properties when exposed to most organic solvents, acids, and alkalis.
Boilpeak’s perfluoroelastomer seals can withstand over 1,800 chemical media tests and offer superior sealing performance. This effectively reduces process defects and particle contamination. In semiconductor wafer manufacturing and other industries with highly corrosive chemicals, Boilpeak’s perfluoroelastomer seals provide exceptional chemical resistance, heat resistance, and ultra-high cleanliness. Additionally, in advanced nanotechnology processes, Boilpeak’s full range of products performs excellently, maintaining a leading position in the market.
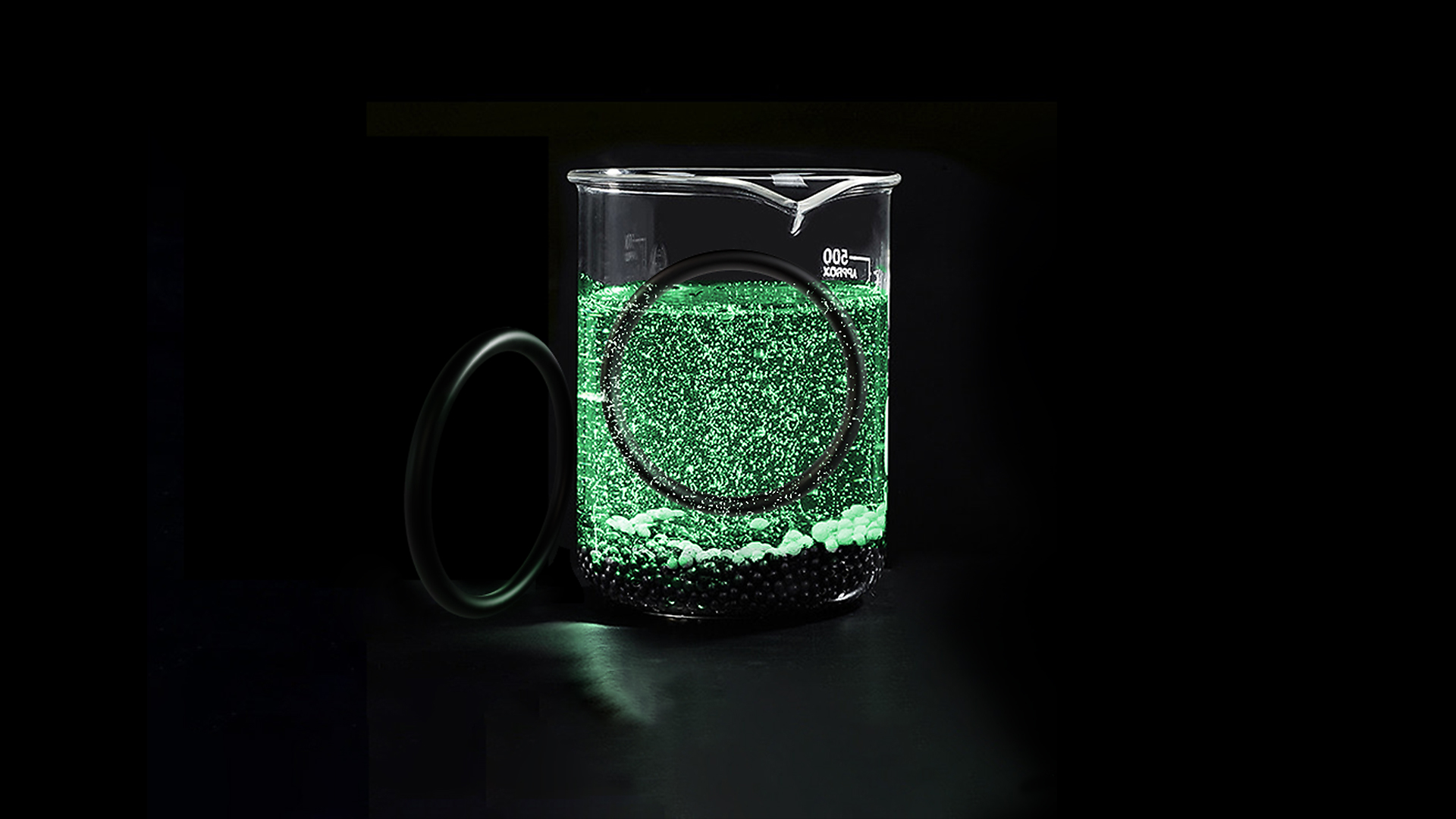
Chemical resistance is high
With excellent chemical resistance, iteffectively extends the product’s lifespan
Global Compatibility
The products developed by Boilpeak are selected based on the continuously growing popularity of existing models.
Sealing Technology
Leading advanced processes to achieve next-generation nano high-purity sealing technology
Corrosion-resistant process applications
BOILPEAK has more than 10 years of excellent manufacturing experience, and keeps pace with the times with continuous development and innovation. Facing the harsh process conditions, we are committed to providing various solutions and continuously developing new special elastomer materials to provide the best sealing
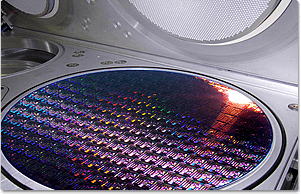
Thin Film Process
The thin film process can be divided into two deposition methods: CVD (Chemical Vapor Deposition) and PVD (Physical Vapor Deposition). Both deposition methods pose different challenges for sealing applications in the process.
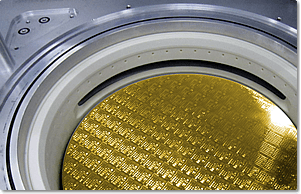
Etching Process
The etching process environment is categorized into Dry Etching and Wet Etching. The primary use of high-intensity plasma and various chemicals in the etching process poses different challenges for sealing applications.
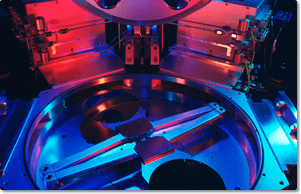
Diffusion Process
The diffusion process can be divided into Ion Implantation and Diffusion. The primary use of extremely high temperatures and various chemicals in the diffusion process poses different challenges for sealing applications.
High-purity product range
BOILPEAK extensively innovates O-rings and related products, working with customers to identify excellent combinations for industrial applications from China.
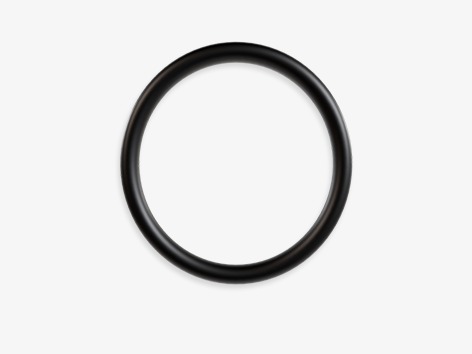
UTpure™ KS291
Product Features:
Excellent resistance to harsh chemical solvents
Extremely low metal ion content
Minimal residue in solvents
Good mechanical performance under low pressure
Product Applications:
Wet etching
Photolithography development
Wafer cleaning
Liquid pipeline transmission
Product Processes:Wet Etch、Pumpline、Filter
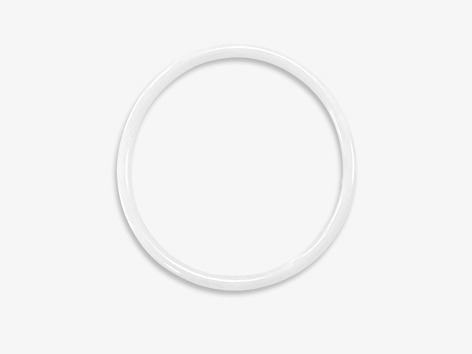
UTpure™ KS235
Product Features:
Excellent resistance to harsh chemical solvents
Extremely low metal ion content
Minimal residue in solvents
Good mechanical performance under low pressure
Product Applications:
Wet etching
Photolithography development
Wafer cleaning
Liquid pipeline transmission
Product Processes:Oxidation、Diff、ALD、LPCVD
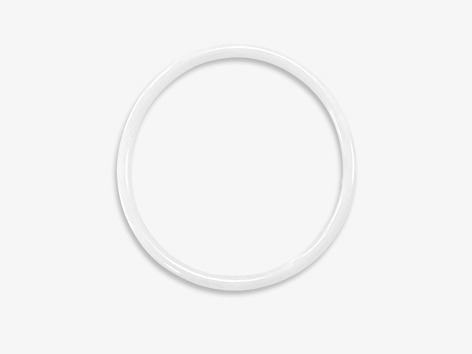
UTpure™ KS732
Product Features:
High hardness, wear-resistant, and self-lubricating
Excellent plasma resistance
High-pressure sealing stability
Low gas permeability
Product Applications:
Gate valve seat sealing
Control valve / butterfly valve sealing
Dry etching chamber
Stop valve sealing ring
Product Processes:Dry Etch、PVD
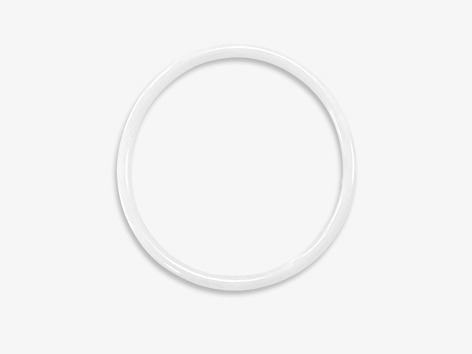
UTpure™ KS130
Product Features:
Excellent plasma resistance
Sealing stability under high vacuum
Cost-effective with good economic benefits
Stable back pressure resistance
Product Applications:
CVD pipeline gas discharge
Plasma chamber sealing
Gas inlet and outlet sealing
Isolation valve sealing ring
Product Processes:Wet Etch、Dry Etch、Pumpline
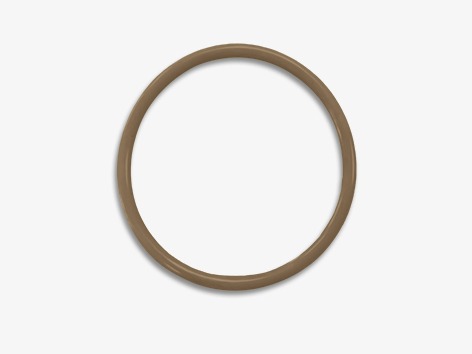
UTpure™ KS291
Product Features:
Excellent plasma resistance
High-pressure sealing stability
Low gas permeability
High cleanliness
Product Applications:
CVD pipeline gas discharge
Plasma chamber sealing ring
Gas inlet and outlet sealing
Dry etching sealing ring
Product Processes:Dry Etch、PVD
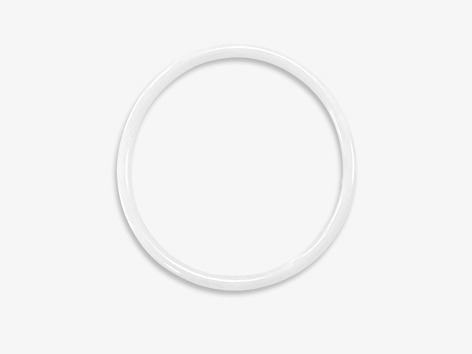
UTpure™ KS291
Product Features:
High hardness, wear-resistant, and self-lubricating
Excellent plasma resistance
High-pressure sealing stability
Low gas permeability
Product Applications:
High vacuum etching chamber
Gate valve seat sealing
Control valve / butterfly valve sealing
Dry etching chamber sealing
Product Processes:Dry Etch、PVD